Opening remarks (Zach Kirkhorn)
- Big focus for Tesla over recent history is expansion and globalization of Model Y program
- Investor Day will be broken up into 5 parts
- “What does it take to to convert Earth to sustainable energy generation and use”
Master Plan: Part 3 (Elon Musk & Drew Baglino)
- Tesla’s big goal is to show that there is a clear path to sustainable energy on Earth without destroying ourselves or the planet
- Detailed white paper will be published with their assumptions and calculations
- Over 80% of global energy comes from fossil fuels
- Half problem statement of fossil fuel economy
- 240TWh of battery energy storage to achieve that (combination of EVs and stationary storage)
- 8:1 ratio assumed meaning for 30TW of power we need 240TWh of energy storage
- This is not a big number relative to the global economy
- Electric economy will mine less ore than with fossil fuel economy
- All forms transportation (minus rockets) will go electric once energy battery production ramps enough
- All cars will go autonomous and electric, only a matter of time
- Conservative estimate based on assumptions around fleet size
- In reality fewer vehicles will be needed thanks to autonomy
- Heading rapidly towards autonomous & electric future
- Model 3 can go one mile on the same amount of energy it takes to boil a pot of water for pasta, and another to cook the pasta
- Modern EVs are extremely efficient
- Heatpumps are air conditioners in reverse that will be used to displace fossil fuel heat sources in homes
- At some point they might make heat pumps for homes
- Hydrogen could replace coal for things like steel production
- Needed for industrial processes
- Shipping accounts for 3% of global CO2 emissions
- Even w/ LFP long haul ships can be electrified
- Short haul planes easily doable, long haul flights will be in reach soon enough
- Long haul ships & planes need to be redesigned and switched to a different architecture to take advantage of electrified fuel source
- 450wh/kg is needed to convert long haul planes & ships to electrification and it already exists
- Tesla wants to produce 1TWh of energy per year as soon as they can
- Building a sustainable energy economy is less than sustaining existing fossil fuel economy
- Only requires 0.2% of available land
- Switching would dramatically reduce impact to environment
- 68 Gigatons of ore every year with fossil fuel economy
- Greatly reduced with switch to sustainable economy
- As we extract resources, we find more
- As Tesla has continued to grow, more core resources have become available
- Vast majority of heavy lifting in terms of electrified transport can be achieved by lithium iron phosphate batteries
- Only long range vehicles need nickel-based Lithium batteries
- Recycling efforts will make this ramp require less and less mined ore over time
Vehicle Design (Franz von Holzhausen & Lars Moravy)
- Today Tesla produces cars differently than they did 10 years ago
- Starting building cars around the following process: Design -> Engineering -> Manufacturing
- Able to combine design, engineering, manufacturing process with the Model 3
- Things didn’t go as planned which resulted in production hell
- Model 3 is the best selling EV ever, Model Y fast approaching
- With Cybertruck they changed the game by starting with manufacturing process which then fed into the design process
- Stainless steel opens up many doors for Tesla since they don’t have to paint them, panels don’t need to be stamped, etc.
- Product Development Process now looks like this:
- Everything rolls up in one organization in Tesla
- This process was first created by Ford over a hundred years ago
- Very clunky for example doors are attached, removed, and then re-added once interior and glass is installed during the production process
- With Model Y structural pack they began dramatically simplifying production by about 10%
- Final process will look something like this
- Only paint sides and parts that need it
- Refer to this as the unboxed process
- New process results in 40% reduction in footprint
- Faster, less capex, more units per dollar
- Can reduce costs as much as 50%
- Next gen platform will be unveiled at a later date
Powertrain (Colin Campbell)
- Plaid is faster than a Porsche, more efficient then a Prius
- Model Y has most efficient EV SUV powertrain on market
- Tesla was able to do this by designing entire vehicle and factory under one roof
- Tesla’s homegrown charging package can handle 2x as much heat as anything available on the market today
- Tesla was able to cut costs and mass of charging package from original Model S in half thanks to advancements & expertise in high powered electronics
- Tesla wrote their own motor simulation software which allowed them to quickly iterate through millions of drive unit designs
- Engineer who designs components are always in same room as people responsible for manufacturing them
- Tesla has figured out how to use 75% less Silicon carbide transistors
- Nobody close from a cost perspective for drive units
- Next powertrain factrory will be 50% smaller with same output as current
- No rare earth materials at all required for new drive units (permanent magnet)
Electronic Architecture (Pete Bannon & David Lau)
- Over 300 low voltage devices (glovebox lights, airbags, etc.)
- Wiring harnesses present a lot of problems especially during initial development
- Reduced wiring harnesses by 17kg from Model S -> Model 3
- Combined controllers to reduce wait and ease manufacturing
- Model 3 controllers were enhanced and added to Model Y and then reintroduced back to Model 3
- Same controllers were updated and leveraged in refresh Model S & X
- Tesla designs 85% of controllers in Cybertruck and will give them advantage in supply chain-constrained world
- Control includes control over software and features nobody thought of originally
- In 2017 they deleted relays & fuses from car in favor of E-Fuses
- E-fuses replace moving parts with solid state transistors that provide fine grained control of power system to software & allow software to do advanced things like load shedding in adverse conditions
- Software controlled hardware is fundamentally about being able to side step tradeoffs with a particular piece of hardware
- “More of everything”
- Expect Li-Ion low voltage battery to last the life of the car
- Eliminates a major source of failures for Tesla
- Use a new tool-less connector which makes easier to service
- Includes software that allows validation that connector has been installed after a service event
- Been able to dramatically improve the 3 & Y center display:
- Cost has been reduced 24%
- Weight reduced by 12%
- Reduced power by 33%
- Increased brightness by 50% while also improving color accuracy
- Demand for in-car power is substantial at around 200A meaning thick wiring harnesses to achieve this with 12V architecture
- With Cybertruck and future platforms Tesla will be moving to 48V which reduces current factor by 4
- 16X reduction in lost power, small wires, smaller e-fusers, smaller heatsinks (or removed completely), etc
- 48V is future for low voltage design at Tesla and rest of industry
- Amount of wiring in cars is driven by number of endpoints
- With Cybertruck, Tesla is moving to a local controller where the wire is connected to nearest controller and controllers are connected via ethernet
- Design has eliminated most of cross car wires in Cybertruck and with next gen platform they all will be eliminated
- Consolidated vehicle network allows Tesla to make some pretty clever changes on the fly without redesign
- You can see the entire vehicle with this architecture
Software (David Lau)
- OTA updates and data insights gives Tesla ability to iterate quickly & maximize impact per iteration
- Example: Monitor usage of sunroofs and eliminate them based on that
- Have ability to harvest real world crash data and make vehicles safer
- Everyday they collect data for 123M miles of driving and 1.9M charge sessions
- Allows them to fine tune battery sizes in future products
- Use collected data to map out rough roads and adjust suspension on Model S & X accordingly
- Before this was sent out to customers, it was pushed out to vehicles in the real world to see how it would perform
- With Model S they realized there are a lot of ways to miss things when manufacturing (pull part from wrong bin, miss connecting wires, etc.)
- “Test early, test often”
- When a production associate plugs something into the car, the software now automatically confirms it is the right part, installs software update if necessary, runs calibration, runs tests, and if problems are experienced calls humans for help
- Service is treated the same way where they are using AI to automatically transcribe customer issues, problem solve, and order parts as a result
- In 2021 Tesla added ability to share vehicles with others
- In 2022 Tesla introduced cloud profiles which allowed driver settings to be shared across vehicles
- Internally Tesla has an app that allows employees to locate and drive all Tesla-owned vehicles at their site
- Loaner vehicles are now getting added to customer’s account so cloud profiles sync and the experience is completely seamless
Full Self-Driving (Ashok Elluswamy)
- Ashok has been working on FSD for 9 years now at Tesla
- FSD is a critical part in a sustainable future as it allows vehicles to serve other customers to benefit society when their owners aren’t using them
- FSD is one of the hardest real-world AI problems out there currently
- Tesla has made significant strides in developing one of the most general systems available
- Architecture
- Tesla is betting on AI mission learning NNs to build a general vision & planning system
- In old days they had single camera, single frame NNs
- Very brittle and struggled in many scenarios
- Tesla in 2022 transitioned stack to multi-camera NNs which take in live feed from car (8 cameras) and produce a single, unified 3D output space
- Reach out to techniques outside computer vision such as language modeling
- Using technologies such as transformers to make system more accurate & computationally efficient
- Even planning system is not stuck in old way (C++) and now uses NN-based planners
- These are needed in complicated urban environments where lots of objects are present & interacting with us
- If we did this using old approach, each approach would take 10ms and likely 1000 approaches would be needed
- Now joint planning can be achieved in 50ms
- Data
- Built auto labeling pipeline that Collects data from fleet, runs computational algorithms in data centers, and produces labels to train these networks
- Data alone can improve corner cases for example in phantom braking scenarios
- Compute
- Massive amounts of compute is needed to continuously train these models
- 30PB of video cache growing to 200PB
- These numbers will increase as Dojo training computer comes online
- FSD Beta has been shipped to 400,000 customers in US & Canada
- Hired a world class team to execute on FSD vision
- Requires human assistance for now but that will change in the future
- Architecture
Optimus (Elon Musk)
- Optimus v2 which wasn’t even functional during AI Day is already well on its way and now able to walk around & perform functions
- Goal is for Optimus to be able to learn based on demonstration or verbal instructions
- Actuators need to be custom designed for humanoid robots
- Designed by same powertrain team that designed Plaid drivetrain
- Might exceed 1:1 ratio of humanoid robots to humans
- Elon is not sure what an economy means at that point
- Elon expects Optimus to be much more valuable than the car business long term
Charging (Rebecca Tinucci)
- A great charging experience is the lynchpin to EV adoption
- 99% road trips possible, 1.5M weekly supercharging sessions, 99.9% site-level uptime
- 9TWh of charging provided in 2022
- 80,0000 charging points including 40,000 Superchargers
- Industries lowest deployment for charging locations (AC & DC)
- Superchargers are prebuilt at Giga New York
- Trip planner allows Tesla to load balance Supercharger locations and drive up site usage without risking wait time
- Projecting site occupancy based on what vehicles are routing to it with ultimate goal of being air traffic controller for all EV charging needs
- 50% of European Supercharger locations are open to 3rd party EVs, 10 sites in US
- Supercharger v4 are now being installed in Europe and come with longer charge cables which are more friendly for 3rd party EVs
- Tesla is trying to capture as much renewably generated energy and leverage that for charging
- This means day time charging and as a result they are installing more AC chargers since speed isn’t as big of a factor for this use case
- Need to scale industry capacity to 9PWh on an annual basis
- Wireless induction charger introduced
Supply Chain (Karn Budhiraj, Roshan Thomas)
- Tesla engineers typically have to map out new parts to the point of being onsite with suppliers to help them bring up manufacturing lines
- Tier 1 means parts that are required to build products in Tesla’s 5 factories
- Tier 2 means supplier of suppliers
- With batteries Tesla works with various degrees of suppliers including tier 6 (mining)
- Management of Tier 2 suppliers is where Tesla excels
- In-vehicle computer is one example of why Tesla needs to focus on both tier 1 & tier 2 suppliers since it is comprised of so many different components
- Moved about 16 million pallets from suppliers to Tesla factories (would cover half the circumference of the earth)
- Tesla’s approach is to bring manufacturing of sub components to point of consumption (really helped them get through COVID)
- These figures assume most pessimistic figures and no simplifications
- No supply chain constraints to get to 20M vehicles per year
- Tesla introduced Model Y heatpump at start of pandemic, the team had 100 components with many different suppliers
- Tesla quickly iterated from manual lines -> semi-automated lines -> simulated further automation (3D simulation) -> fully automated lines
- Full automation of heatpump production line only took 8 months
- 99% reduction in labor
- 99.9995% quality
- 7 seconds between each heatpump produced
- Strategy going forward
- Fewer parts, fewer components
- Do more with less
- Deep involvement with suppliers
Manufacturing (Tom Zhu, Drew Baglino)
- 4 vehicle factories
- 65,000 manufacturing employees (including Giga Nevada)
- ~2M current annual build capacity but growing all the time
- Completed Giga Shanghai in 9.5 months
- Leveraged straight manufacturing lines with limited curves to simply factory construction (amongst other benefits)
- In house construction team that is used to build these massive factories (built Giga Berlin, Giga Nevada, and Giga Texas)
- 4,000,000 Tesla vehicles were produced as of today and just so happened to be produced at Giga Texas
- 7 months from 3M to 4M vehicles (exponential growth)
- The plan was to get a new vehicle to roll off the line every 45 seconds
- Fremont just yesterday set a daily production record
- Build factories aligned with the following philosophy
- Question -> Delete -> Simplify -> Accelerate -> Automate
- Learning from both new & old factories
- Giga Berlin recently implemented 5G to make one process more efficient
- 4 factories is not enough to reach 20M however with the internal Giga Factory team they’ll be able to scale this out
- Made a lot of progress with manufacturing including that of cells (full automation)
- 5x reduction in factory footprint from 2170 cells to 4680 cells
- 10x smaller factory volumetrically
- 50GWh/year Corpus Christi Lithium Refiner will start commissioning end of 2023 (ground breaking to commissioning in 10 months)
- Designed to ingest Lithium spodumene
- On top of this Tesla is working on their 60GWh Cathode factory which will be commissioning in Q2 2023
Energy (Mike Snyder, Drew Baglino)
Have built a software & hardware platform that can adapt to be used anywhere in the world
Tesla is on their 6th generation of their industrial energy products
16GWh of energy storage products deployed to date
Lathrop factory continuing to ramp & scale
Megapack XL is the most energy-dense storage solution on the market at 300 MWh / acre
- 2x more dense as gas peaker plant
Power electronics are critical to the entire mission
Virtual machine mode acts as a shock absorber to grid events
- One grid operator will not convert to 100% renewables unless they get this particular feature working
Autobidder is an autonomous energy trading platform that allows folks to buy energy low and sell it high
- Makes 100s of thousands of decisions per second
- Has proven to be a market leader
First Megafactory (Lathrop) was converted from JC Penny’s distribution center to a factory in less than one year
Increased installation speed by 4x and reduced total labor by 3x
In Australia they were paying consumers to bring their power generation capability to the grid
Coming in July in Texas Tesla is bringing unlimited home charging
- Retail electricity plan
- Reduces TCO of vehicles
- Incentives people to charge at home at night
Demand for energy products is there and thus additional manufacturing capacity is needed
Impact (Laurie Shelby, Brandon Ehrhart)
- 129,000 total employees, almost half of that is involved with vehicle manufacturing
- In 2022 Tesla got 3M applicants for engineering positions
- Sustainability is key to Tesla and as a result their customers avoided the creation of a ton of emissions (equivalent of 1.7M ICE vehicles for 1 year)
- Model 3 even in worst case scenario uses less energy than the average ICE
- More coming in impact report
Financials (Zach Kirkhorn)
- Since introduction of Model 3 production, they have reduced costs by 30%
- Cost reduction will continue to be paired with improvements
- Cost reductions come from anywhere
- Model 3 has a lower TCO than Corolla
- 60-70% lower selling, general, and administrative expenses per vehicle then competitors
- As a result they think more about operating margin vs gross margin
- Tesla is now aligning to Tesla Operating System which will streamline efficiencies across the board
Q&A
- Giga Factory in Mexico officially announced
- Ground breaking will be coming soon in Monterrey
- Existing factories will continue to expand & scale further
- New Unboxed Vehicle manufacturing process will be brought to new products first then put into existing products as time goes on
- Bi-directional charging coming to all Tesla vehicles within next 2 years
- Trying to keep unique vehicle models to no more than 10
- Tom Zhu not concerned about Tesla’s position in China as they continue to cut costs while providing valuable products
- Demand is definitely a function of affordability not desire when it comes to Tesla
- Continues to target excess battery production so they can keep vehicle factories running at full bore while ramping energy storage production as needed
- Over 95% of supply chain in China is localized
- For FSD, Tesla plans to auto label most of the collected data
- Since they want to build a scalable solution, they are going to continue to shy away from HD maps even though they could build something similar with the data & tech they’ve built
- Dry electrode
- Every passing week leads more progress in yields, quality, etc.
- Thanks to overcapacity, they have the ability to experiment as they ramp
- Tesla is operating more than one anode lines and its an internal competition on which process will create the highest yields
- Acquired Maxwell mainly for the dry electrode process
- Plan to scale to volume production by end of year
- Next Generation Platform
- Tesla will host a dedicated event for this product
- Giga Factory in Mexico officially announced
Tesla 2023 Investor Day - 2023-03-01
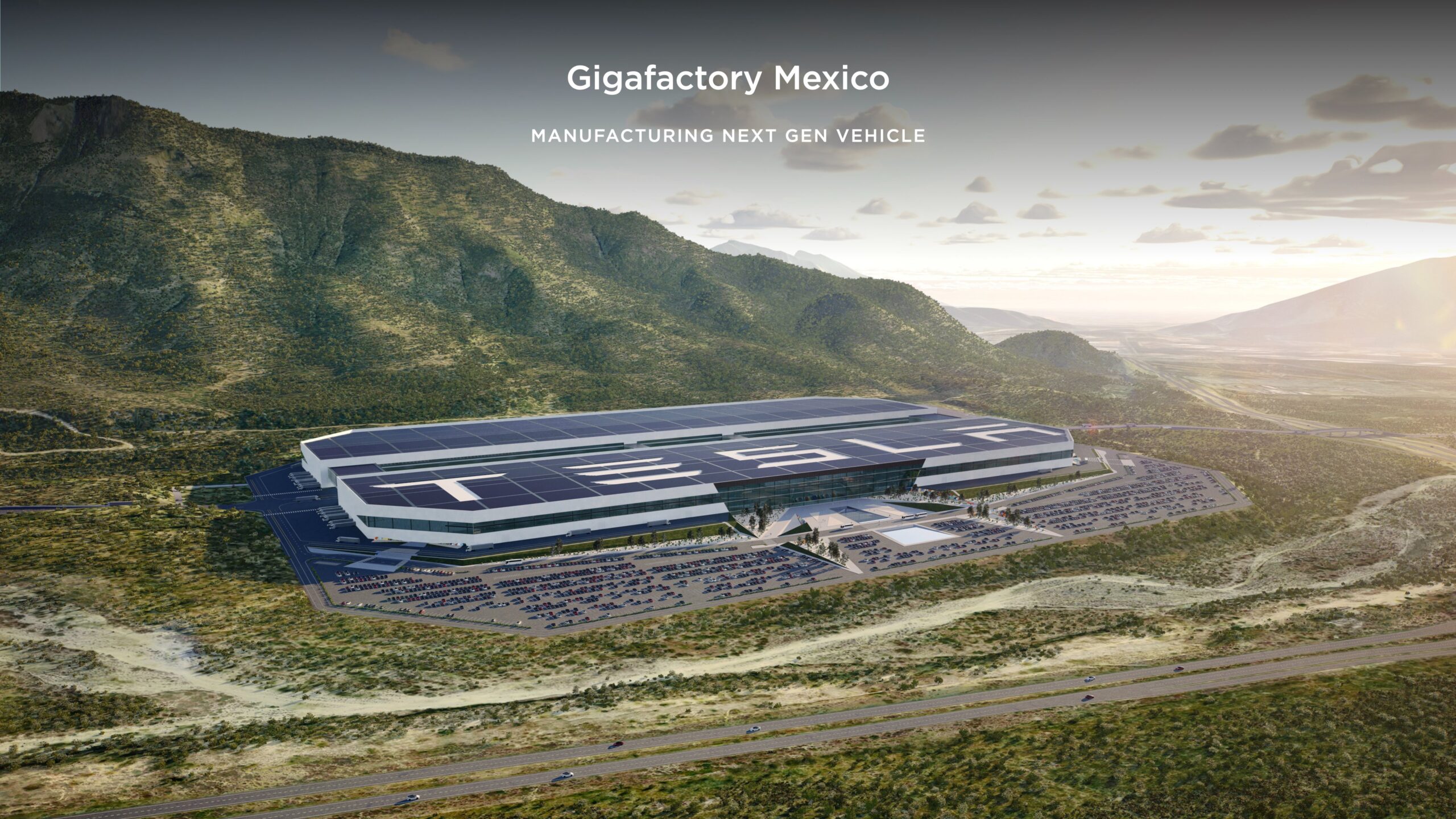